Structural Engineering Spotlight: Getting to Know Nikunj Patel and the Design Process
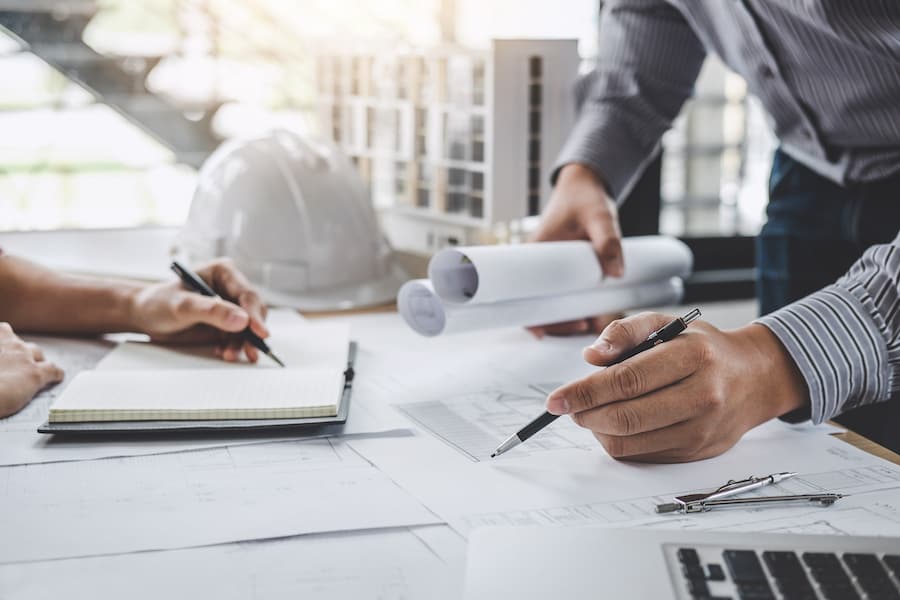
When you build a home or commercial building in Texas, one of the most important aspects you must consider is the type of soil underneath your structure. The clay-based soils in Texas are highly expansive, so they are susceptible to swelling and shrinking depending on the moisture content. Understanding the soil type your foundation will sit on is vital for the design process of the slab, as well as for repairing a slab or pier and beam foundation.
At Perma Pier, we value education and partnering with passionate field experts. We spoke with structural engineer Nikunj Patel about how his firm, Strand AE out of Dallas, goes through the process of designing a foundation slab. From testing the soil to building the slab, there are a variety of factors that go into the process. Here’s what we learned through our conversation.
Pre-Design Process
Before designs even begin, there are several pieces that need to be put together in order to adequately design a slab. In the state of Texas, each city requires a foundation plan to be signed and sealed by a licensed engineer. In order for this to happen, the builder would need to provide a geotechnical report of the specific site and lot the home will be built on.
A geotechnical report provides structural engineers detailed information about the soil, helping them understand the type of soil and the amount of movement occurring within it. This is critical in order to design a slab that will be in accordance with the soil type. The way a geotechnical report is created is by taking samples of the soil, determining its unit weight, its weight without any moisture, and its weight with moisture. This helps the engineers understand how much this specific soil will shrink or swell in certain conditions—known as potential vertical rise (PVR).
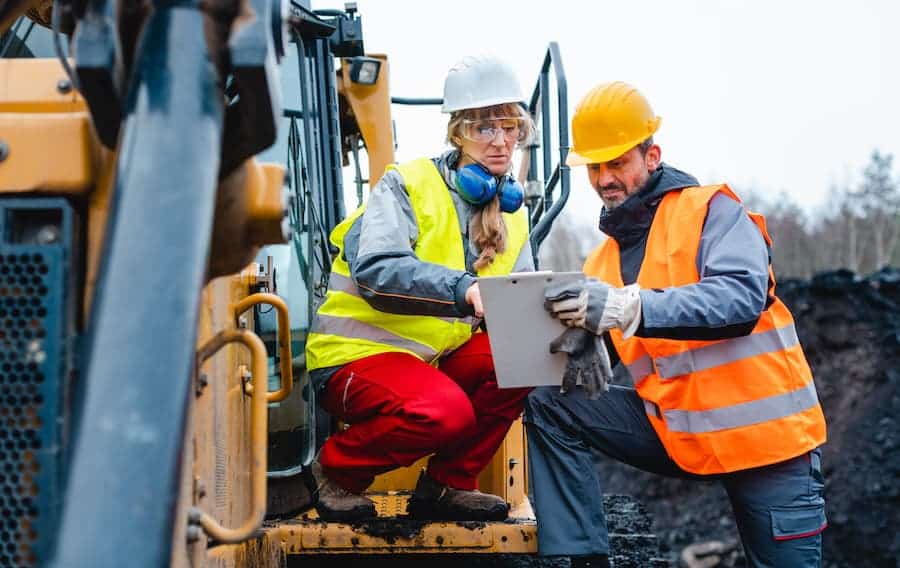
What Does Potential Vertical Rise Mean?
The PVR of a soil is a measurement for determining how active a soil is. Sandy soils without any clay particles are non-active, meaning they’ll settle, rather than shrink. However, expansive soils can have a swelling and shrinking range anywhere from a half an inch to up to nine inches!
In order to design a post-tension slab, there are certain code requirements that must be met. The Post-Tension Institute (PTI) is industry standard and requires the soil be remediated if the PVR is over four and a half inches. This is done in two different ways.
The two most common soil remediation methods include:
- Moisture conditioning: this is done by excavating the soil to a certain depth recommended in the geotech report. Once complete, moisture is put into the soil and placed back in the same spot. Then a poly sheeting is put on top to prevent moisture from evaporating.
- Water injection: injecting high-pressure water down to a certain depth, every certain amount of feet a part and spaced out at certain intervals.
Both of these methods are designed to achieve the same end result. The soil is pre-swelled to the point where they won’t experience any more fluctuation in moisture over the four and a half inches. Essentially, these methods try to mimic what happens in the environment, from extreme wet to extreme dry, in order to provide a baseline for the design of a foundation.
Designing a Post-Tension Slab
Once the pre-design process is complete, it’s time for the actual designing to begin. Every foundation is site and lot specific. With the information from the geotechnical reports, the engineers are able to use it to design the slab for the site. The type of slab they will typically design is a post-tension slab.
Compared to a conventional slab (made with rebar in the beams), a post-tension slab is made by using the same grade beams cut into the grade. However, instead of rebar it is substituted with post-tension cables. These are high-steel coil wire cables, generally a seven coil bunched together, and they are encapsulated in plastic to prevent corrosion within the concrete. Once the cable is installed and the slab is poured, the cables are then stressed.
After the concrete has cured for about five to ten days, the cables are stressed, effectively compressing the concrete and preventing shrinkage cracks. Because the moisture content in the soil can cause a foundation to move, post-tension slabs are designed to ensure there is uniform movement throughout to avoid compromising the structural integrity.
Note that it’s important to understand if the moisture of the soil around your house varies, there can be some stress put on your foundation. Making sure the moisture content around your home is uniform can help prevent differential movement of your foundation, effectively prolonging the life of your foundation.
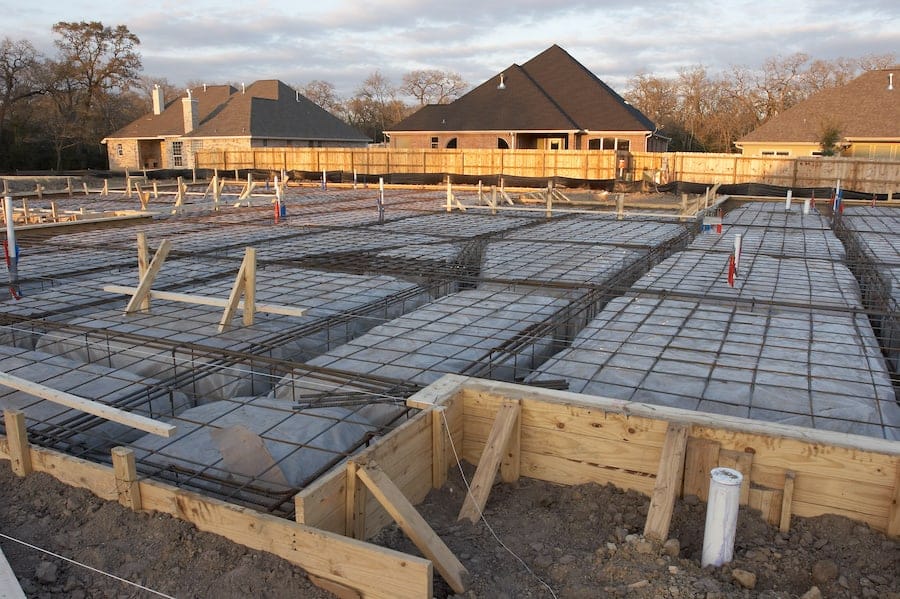
Leading Texas Foundation Repair Company
At Perma Pier, we understand there is no one-size-fits all approach to foundation repair. We also understand the importance of understanding soil types in relation to the health and longevity of your foundation.
Texas has a wide variety of geography, surface geology, and climates, which means there are a variety of soil types, each one affecting your foundation in a unique way. This is why our professional evaluator team has received extensive training in the science behind Texas soils.
At Perma Pier, we know Texas soil. You can trust we have the knowledge and expertise to provide you with the right foundation repair solution for your home. If you’re in need of foundation repair, contact us today for a free evaluation.